切削加工のプロ、榊原工機の榊原社長に突撃して、加工のリアルなところをあれこれ聞いてみるシリーズ。今回は、手間がかかるため業界では敬遠されがちな「単品加工」について、加工の実例とともに詳しく教えていただきました。
単品加工とは
単品加工とは、部品加工において、製品を一つ一つ加工する方法です。製品ごとに工程やプログラムを組み替えて加工するため、特注品や試作品、カスタマイズ製品の製造に向いています。また、装置の部品などで1個ずつの部品を集めて10個、20個でも単品加工と呼んでいます。
「榊原工機は柔軟な生産体制を組んでおり、手のひらサイズの単品加工を得意にしています。社内で加工できない大物や板金は協力会社に依頼することもありますが、基本的にはどんな部品でもワンストップで受けることができます。もしお手元に1個ずつの部品の図面が10枚、20枚あったら、ぜひ当社に丸投げしてください」(榊原社長)
では、実際の加工事例を見ていきましょう。
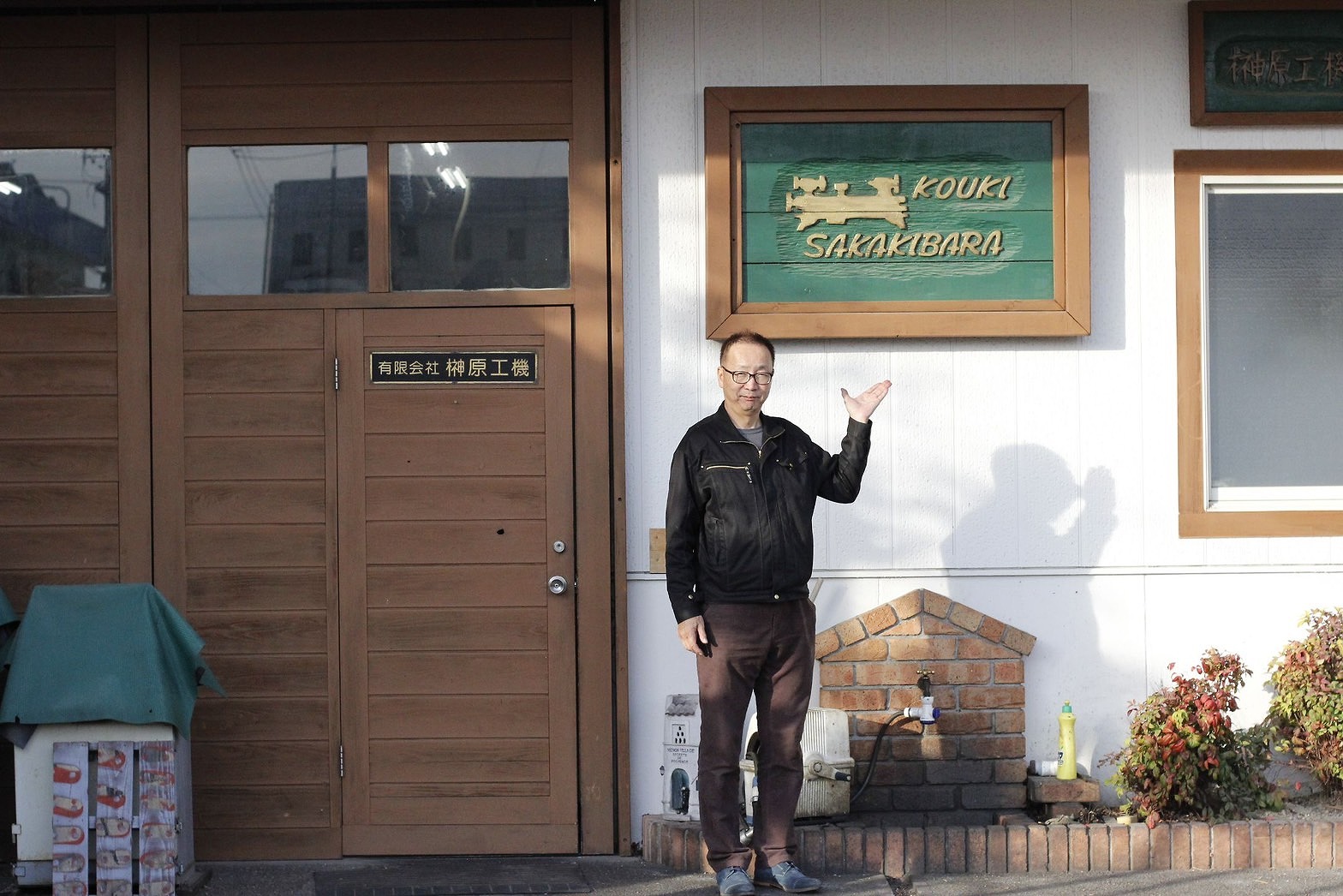
マシニングセンターによる単品加工
マシニングセンターで、曲面の溝入れを行った加工です。
表面(6面)の精度を出す加工がしてある6F材から加工していきます。
最初に外形を切削してから、溝を掘って穴をあける今回の加工は、X軸とY軸の2軸で加工できる形状だったので、2次元のマシニングセンターで加工しました。
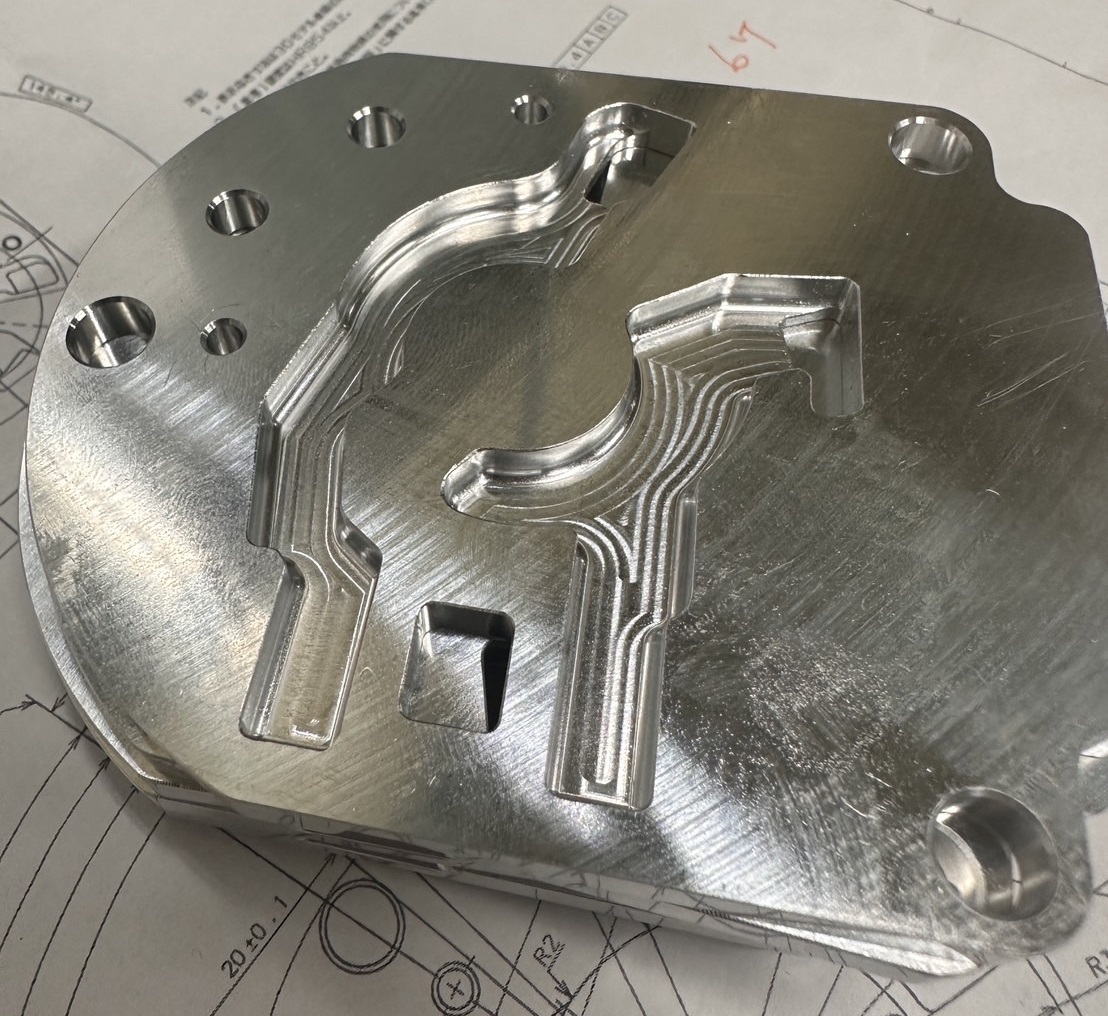
続いては「吸い込み」と言われる部品です。真ん中の溝をお客様の製品が通過する部品ですので、表面の滑らかさ、美しさが求められます。
こちらの加工、シンプルな2次元加工に見えて実は3次元加工です。マシニングセンターで溝と縦穴、タップ穴を加工してから、入口の斜めの部分を三次元のマシニングセンターで加工しました。
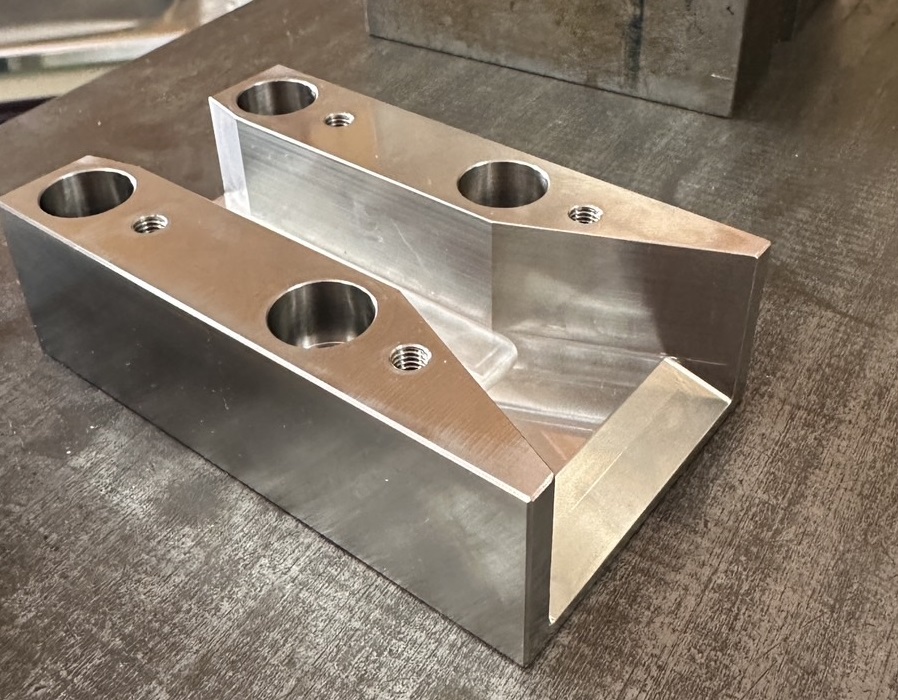
こちらはマシニングセンターによる3次元加工の製造事例で、10個ほどで製作した取っ手部品。このような部品は量産では金型を起こして鋳物で作る方が効率が良いのですが、数が少ない場合は切削加工のほうが効率良く製造できます。
今回は真鍮の素材を、上の面、下の面、ねじの面と4工程に分けて切削加工しています。最後は直径2mmのボールエンドミルを走らせて、仕上げをしています。小さな部品ですが、1個作るのに1時間以上かかっています。
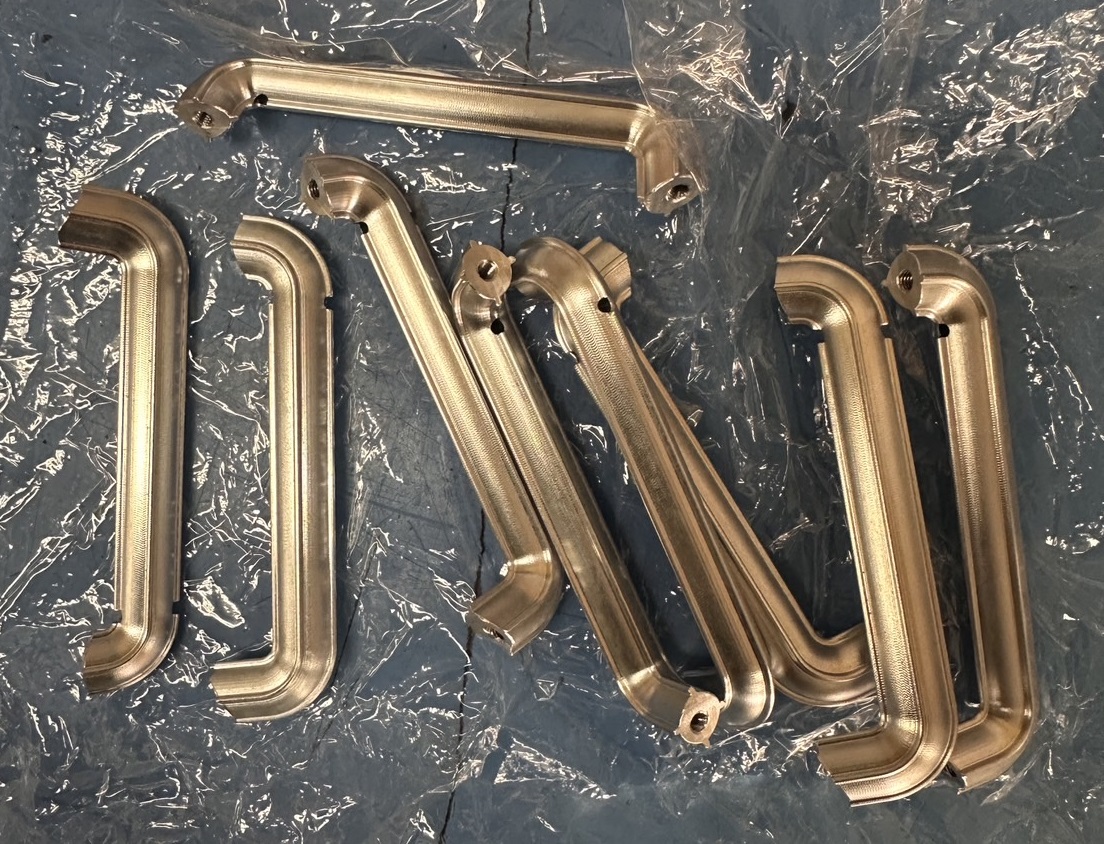
旋盤とマシニングセンターによる単品加工
この部品も1個でご注文いただいて、単品加工を行いました。旋盤の後にマシニングセンターで、2工程で加工しています。
1工程目は旋盤で外周加工、内径加工、溝入れ加工を行いました。
完了後に2工程目のマシニングセンターに移動して、外周にある3箇所の四角い切り欠きと、丸穴をあけました。
当社には1工程で加工できる複合加工もあるのですが、この部品は2工程にしたほうが効率が良く安全に加工できるため、このような工程を組みました。
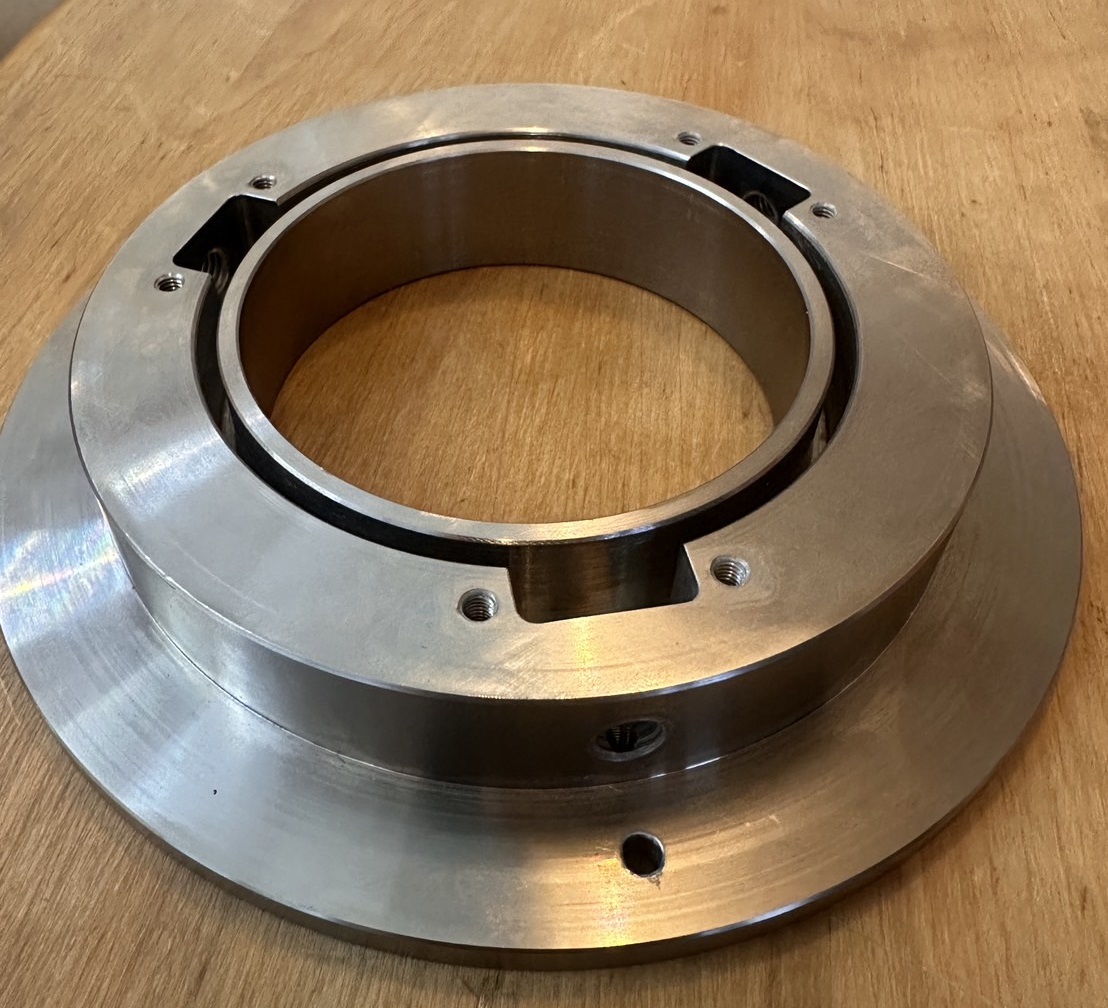
複合旋盤による単品加工
こちらの部品は高い精度が求められる部品でした。工程を分けてしまうと、部品を掴み直す際に位置がズレてしまう可能性があるので、旋盤とエンドミルの加工が1台・1工程で可能な複合旋盤を選定し、ワンチャッキングで加工しました。
外径の切削、ネジ山、溝入れ、穴あけの工程を同軸で加工しているので、ご要望通りの精度を出して納品することができました。
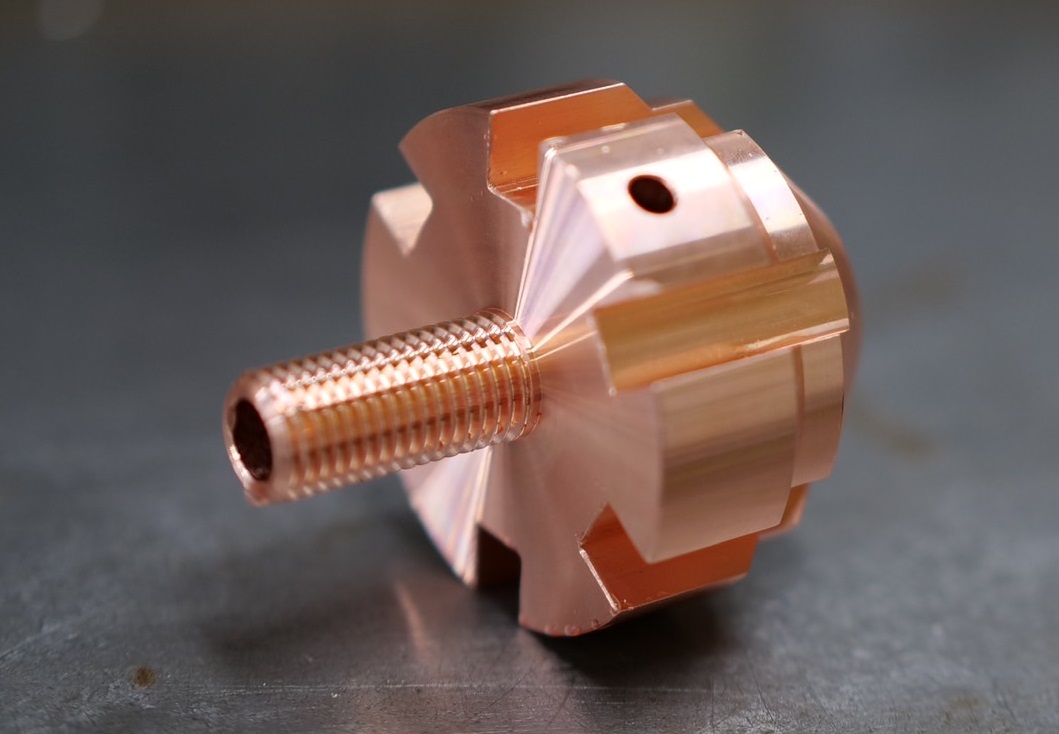
ワイヤーカットによる単品加工
こちらはレーシングカーの部品で、軽量化と高精度が求められる難しい加工事例でした。
最初にワイヤーを通すためのスタート穴をマシニングセンターで開けてから、ワイヤーカットで時間をかけて加工しました。(実は2晩かかりました)
ちなみにこの部品は横の長さが500mmあるのですが、当社にあるワイヤーカット加工機の加工範囲は350mmまで。そこで、右側と左側、2回に分けて加工しました。
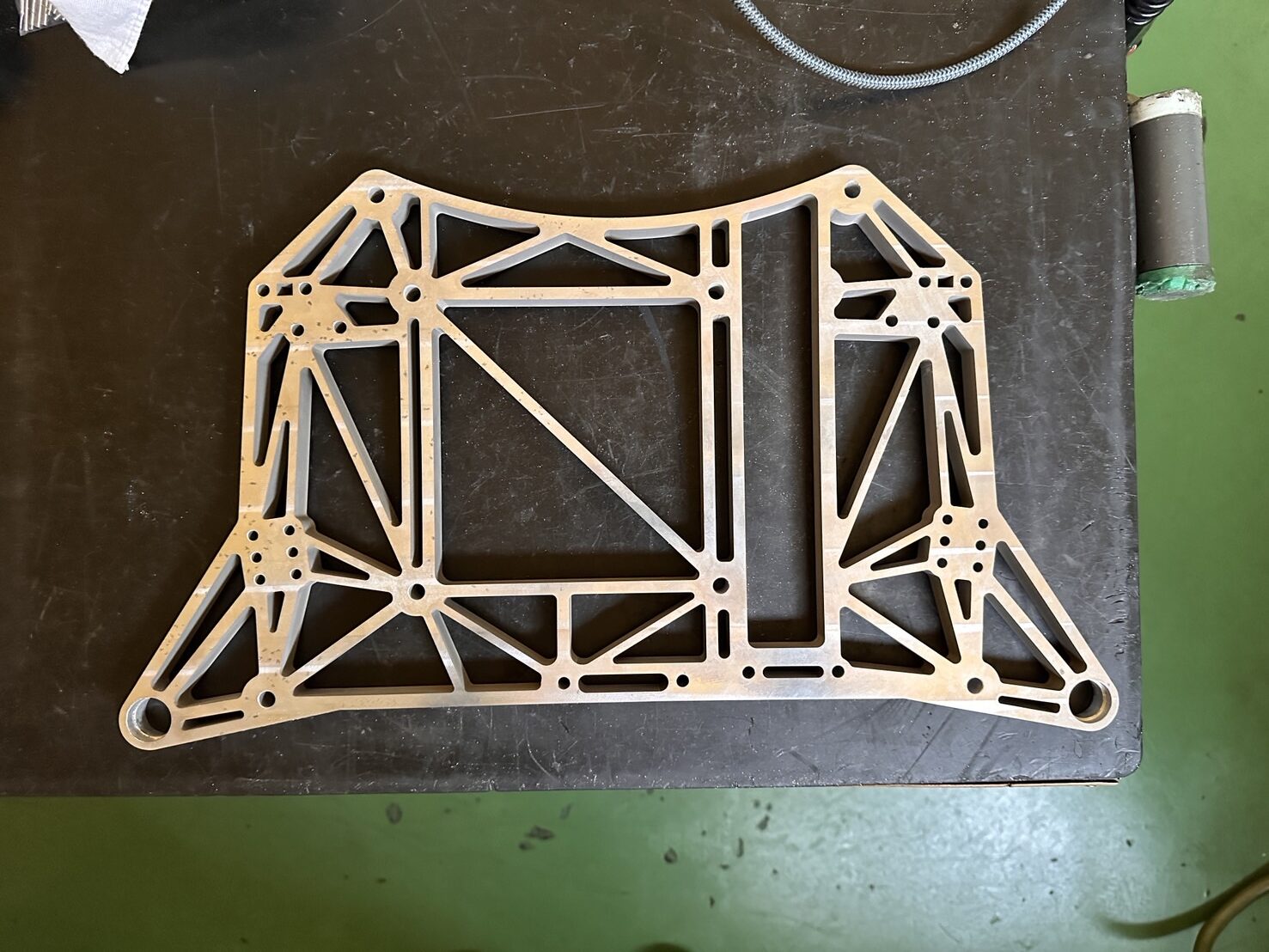
このように、当社は1個~の単品加工、試作品、小ロット品、特急の加工や、単品ばかりの図面の束などがありましたら、ぜひ榊原工機にご相談ください。最短翌日発送で、皆さまのお力になれるようにがんばっております。2024年のゴールデンウイークもカレンダー通りで元気に稼働いたしますので、4月30日、5月1日、2日もご相談お待ちしています。
その他の提案・試作事例
こちらまで